Introduction to pharmaceutical film coatings
A wide variety of pharmaceutical products, including pellets, granules, capsules, powders, and crystals are often film coated. In this present article, we will concentrate on the film-coating of tablets.
The procedure of coating tablets is a complex process that results in the forming of a thin layer around the tablet. This layer is in the range of 20 to 200 μm in thickness, or around 1 to 9% of the initial weight of the tablet. As a reference, a human hair is usually around 100 μm thick, much like the typical thickness of an immediate release coating.
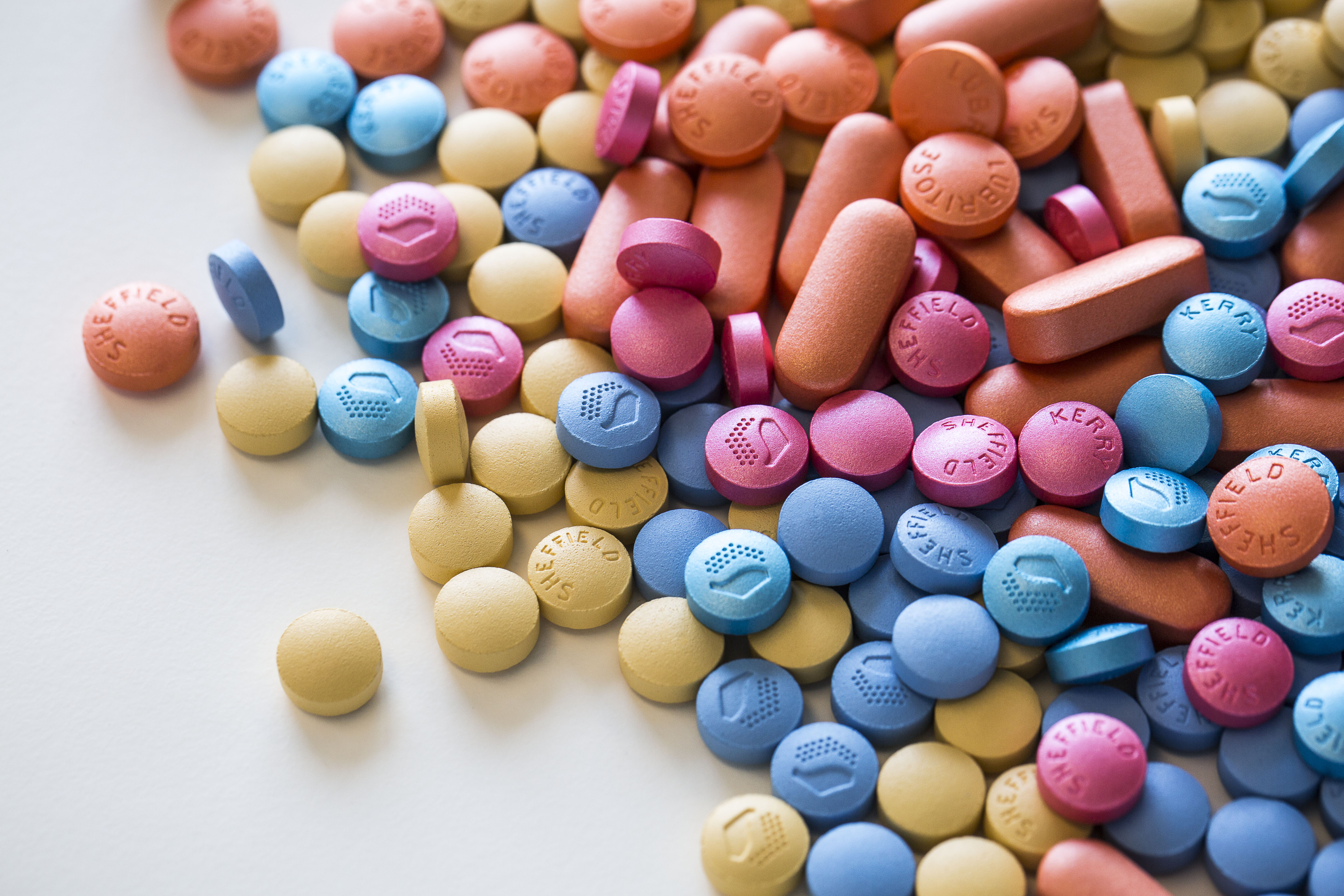
What are the main reasons we coat tablets?
Aesthetic and protective coatings which allow for immediate release of the API
- to increase the shelf life of the tablets as the coating can protect tablets from light, moisture and oxidation
- to improve product appearance and identification. Film coatings may be colored and are an excellent branding, trademarking, and identification (patient safety) tool
- to improve the ease of swallowing by making the tablets smoother
- to improve the strength of the tablet – the coating increases the mechanical resistance of the tablets
- to improve the taste and mask odors associated with APIs, which are often bitter
Controlled release of drug (often referred to as functional coatings):
- making the release of the drug in various GI sites depending on the pH. Example: the enteric or gastro-resistant coating which protects the API of the acidic media of the stomach or protects the stomach from the irritation of the API. an HPMC based subcoating is justified for both isolation and cost reasons before the gastroenteric layer
- prolonged or sustained release may be achieved with special coatings
Some pharmaceutical companies produce their own coating formulas, but many others instead purchase fully formulated powders for reasons of cost-saving, efficiency improvement, and product consistency.
What is the composition of a typical coating formula?
- A pharmaceutical polymer; this is the backbone of the coating layer:
- Cellulosics, such as hydroxypropyl methyl cellulose (HPMC) , Hydroxypropyl cellulose (HPC), and ethyl cellulose (EC)
- Vinyls, such as polyvinyl alcohol
- Acrylics, such as methacrylic acid / ethylacrylate copolymers (often used for enteric or delayed release coatings)
- Natural derivatives, such as shellac or alginates
- A plasticizing agent. This will reduce the film – forming temperature of the polymer and make it possible to apply at lower temperatures, and improve the elasticity of the coating film:
- Polyhydric alcohols, such as propylene glycol or polyethylene glycol (PEG) or glycerol
- Acetate esters, such as triacetin (glycerol triacetate) or triethyl citrate(TEC)
- Glycerides, such as acetylated monoglycerides
- Oils, such as mineral oil or vegetable oils
- Colorants and pigments that increase opacity, light protection and provide coloration:
- Water insoluble lakes: Such as indigo carmine, tartrazine, allura red, and quinoline yellow (water soluble dyes of these same colors may also be used)
- Inorganic pigments: Titanium dioxide, iron oxides, and pearlescent pigments (containing mica)
- Natural colorants: including vegetable juice, carotenoids, and turmeric
- Glidants, which are incorporated to produce coatings which are smooth and tack free
- talc
- waxes, such as carnauba wax
- stearates
- Flavors, which may be used to improve the patient experience or provide brand value
- Sweeteners, which may be natural or high intensity artificial (such as sucralose)
- natural or artificial flavors, such as mint, vanilla, or berry
- Viscosity modifiers, which often allow coatings to be applied in a more efficient process or create an improved tablet appearance
- Carbohydrates, such as lactose, polydextrose, or starch
- Gums, such as acacia or xanthan gum

How are typical coating formulas applied?
The coating process begins with the preparation of a suspension that consists of the coating formulation (primarily solid ingredients) and a liquid solvent which is water, alcohol or an organic solvent. In house formulations prepared from individual components often require the use of multiple mixers and kettles (low shear and high shear mixers) over the course of several hours. In contrast, a commercially supplied, fully formulated film coating is dispersed in water with a low shear mixer, with only approximately 45 minutes of stirring required.
There are a number of coating equipment designs in common use: solid pans, side vented pans, fluid bed machines, fully perforated drums, and continuous coaters. All high performance coating machines utilize effective mixing of the tablets, and efficient drying of the coating solution. During the coating process the prepared coating suspension is sprayed as a pattern of fine droplets onto the surface of the moving tablets, as drying air passes over and through the tablets. The solvent portion of the coating preparation will evaporate, leaving a thin layer of coating adhered to the surface of the tablets.

What are the recommendations regarding the core tablets?
As the coating procedure is a serious stress factor for the tablets, especially for batches in excess of several hundred kilograms, there are requirements to consider:
- Tablet breaking force is recommended to be over 100N
- Tablet friability should be lowest possible and ideally lower than 0.1%
- Tablets should not have flat surfaces, as they tend to stick together, causing “twinning” during the coating process. A shallow or deep concave is a good compromise.
- Tablets should be free from sharp edges, which can be chipped during the tumbling in the coating pan. A double radius tablet design is be beneficial
- Tablets should be formulated carefully with regards to swellable excipients, and excessive amounts of disintegrants should be avoided, as they may result in pinholes or erosion during coating.
- Tablets should be formulated carefully in order to provide a good surface for coating adhesion. Excessive amounts of magnesium stearates may result in coating adhesion issues, reduced hardness of tablets, and slow dissolution of the API. It is recommended to use the lowest amount possible for tablet production, or substitute it with self-lubricating excipients, such as
- Tablets will expand slightly following compression, so it is advisable to wait a day between compression and coating in order to avoid crack formation in the coating film.
Illustrative Blog Post for pharmaexcipients.com – Prepared by Kerry by Tony McGorisk — All Rights Reserved
Tony McGorisk is the European Commercial Director of Kerry Ingredients & Flavours, a leader in taste and nutrition for the global food, beverage and pharmaceutical industries. He has over 18 years of experience working in the Pharmaceutical Industry. He can be reached at [email protected]
What is the definition of the ideal pharmaceutical coating process?