Optimizing environmental sustainability in pharmaceutical 3D printing through machine learning
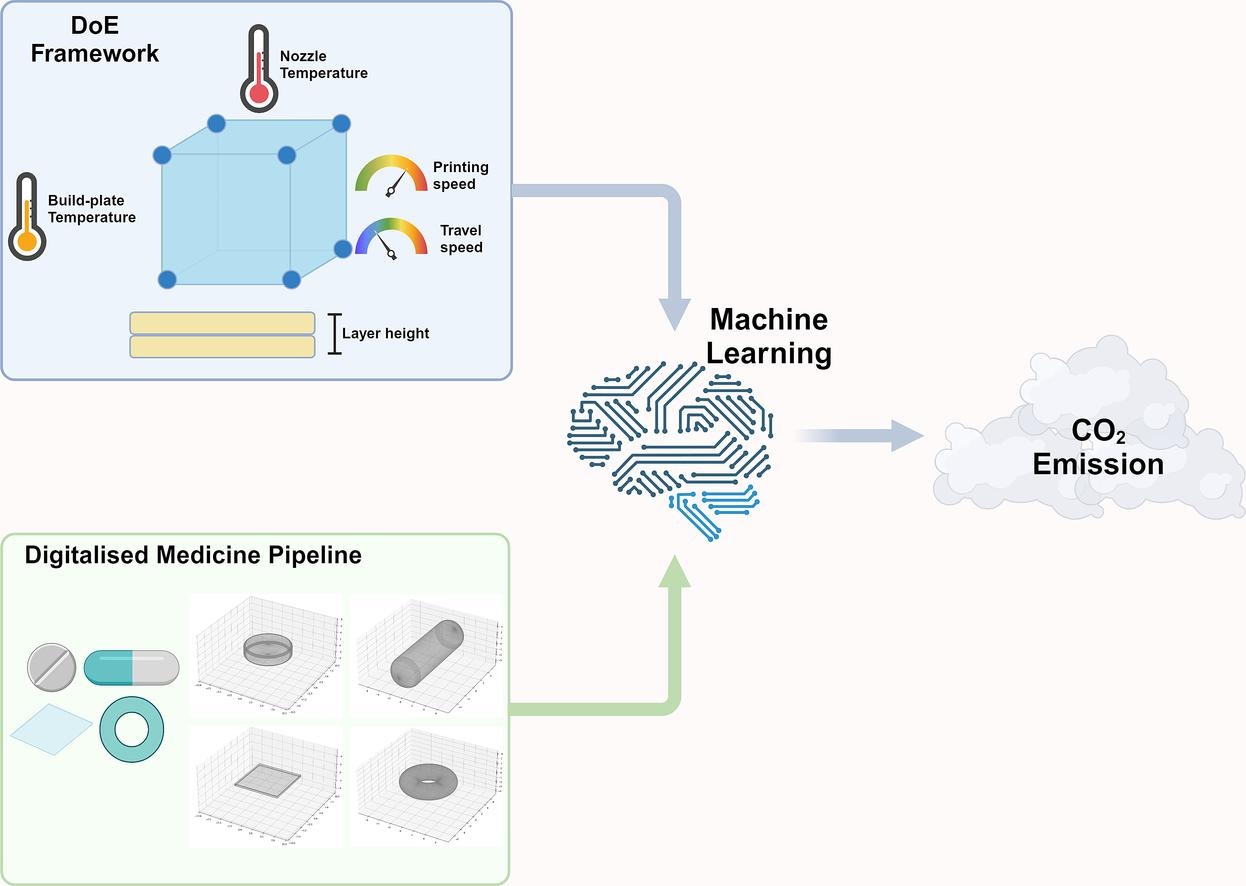
Abstract
3D Printing (3DP) of pharmaceuticals could drastically transform the manufacturing of medicines and facilitate the widespread availability of personalised healthcare. However, with increasing awareness of the environmental damage of manufacturing, 3DP must be eco-friendly, especially when it comes to carbon emissions. This study investigated the environmental effects of pharmaceutical 3DP. Using Design of Experiments (DoE) and Machine Learning (ML), we looked at energy use in pharmaceutical Fused Deposition Modeling (FDM). From 136 experimental runs across four common dosage forms, we identified several key parameters that contributed to energy consumption, and consequently CO2 emission. These parameters, identified by both DoE and ML, were the number of objects printed, build plate temperature, nozzle temperature, and layer height. Our analysis revealed that minimizing trial-and-error by being more efficient in R&D and reducing the build plate temperature can significantly decrease CO2 emissions. Furthermore, we demonstrated that only the ML pipeline could accurately predict CO2 emissions, suggesting ML could be a powerful tool in the development of more sustainable manufacturing processes. The models were validated experimentally on new dosage forms of varying geometric complexities and were found to maintain high accuracy across all three dosage forms. The study underscores the potential of merging sustainability and digitalization in the pharmaceutical sector, aligning with the principles of Industry 5.0. It highlights the comparable learning traits between DoE and ML, indicating a promising pathway for wider adoption of ML in pharmaceutical manufacturing. Through focused efforts to reduce wasteful practices and optimize printing parameters, we can pave the way for a more environmentally sustainable future in pharmaceutical 3DP.
Introduction
Three-dimensional (3D) printing, also known as additive manufacturing, has emerged as a transformative technology in various industries, including pharmaceutics. Its ability to generate complex structures and customized formulations has created new opportunities in drug delivery and personalized medicine (Govender et al., 2021, Seoane-Viaño et al., 2021, Tracy et al., 2023, Yang et al., 2023a). This include polypills (Robles-Martinez et al., 2019), films (Elbadawi et al., 2021, Sjöholm and Sandler, 2019, Xu et al., 2023), microneedles (Li et al., 2021, Wu et al., 2020), scaffolds (Budharaju et al., 2023, Curti et al., 2020, Elsayed et al., 2019), and medical devices (Tan et al., 2022, Xu et al., 2021). The advantages of 3D printing extend to the potential of point of care manufacturing and production of small batches (Bastawrous et al., 2022, Biglino et al., 2023, O’Donovan et al., 2023, Yang et al., 2023b), potentially reducing the amount of material waste and transportation impact on the environment. However, like all manufacturing processes, 3D printing has an environmental impact because of the carbon emissions generated during printing and the potential use of hazardous materials and chemicals (Kechagias and Chaidas, 2023, Malik et al., 2022). Since 3D printing has huge potential as the next major method of pharmaceutical production, now is the time to develop sustainable practices and strategies that minimize its ecological footprint and promote responsible manufacturing processes.
3D printing is an overarching term that encompasses seven main technologies: binder jetting, vat photopolymerization, powder bed fusion, material extrusion, material jetting, directed energy deposition, and sheet lamination, with material extrusion being the most investigated category (Bouzaglou et al., 2023, Nikitakos et al., 2020). Fused Deposition Modelling (FDM) is a subset of material extrusion that operates on the principle of layer-by-layer extrusion of filaments to create the 3D object. It is the most commonly studied technology for pharmaceutical fabrication (Azad et al., 2020; Cailleaux et al., 2021; Shaqour et al., 2020). Melt-Extrusion Deposition (MED®), a derivative of FDM developed by Triastek, Inc., is a 3D printing technology that uses a temperature-mediated process to create layered structures for drug delivery. Triastek’s 3D printed product, T19 has recently gained FDA IND status (Wang et al., 2023). Hence, it possesses the potential to be translated into both clinical and manufacturing settings.
In FDM, a thermoplastic filament, such as polylactic acid or polycaprolactone, is fed into a heated nozzle where it is melted and then precisely deposited onto a build platform, forming successive layers until the final object is formed (Melocchi et al., 2020). It is essential to control the printing parameters (infill density, layer height, printing speed, built-plate temperature and nozzle temperature) to achieve an optimal product. Filaments used in FDM are mainly prepared using hot melt extrusion (HME); hence, unlike other 3D printing technologies, the FDM production pipeline comprises two process steps rather than one. Both FDM and HME operate at high temperature, and so they have higher energy consumption demands than printers that operate at room temperature (Elbadawi et al., 2023).
The need to achieve environmentally sustainable practices are driven by multiple large economies and governments seeking to achieve carbon neutrality within the next few decades. Collective policies are rapidly ushering in a new industry paradigm that is rapidly transforming Industry 4.0 to 5.0. In the context of industrial transformation, Industry 4.0 marked a significant phase characterized by the integration of digital technologies and automation in manufacturing and production processes. In contrast, Industry 5.0 represents a novel evolution that elevates this transformation to a higher level, emphasizing the amalgamation of digitalization with an intense commitment to sustainable practices and social responsibility (Grabowska et al., 2022). The implementation of socio-economic policies plays a pivotal role in driving this paradigm shift, requiring industries to integrate sustainability and social responsibility as fundamental elements of their operational strategies. Notably, this shift is evident in the adoption of cutting-edge technologies by industries to optimize energy consumption, reduce waste, and uphold circular economy principles (Chauhan et al., 2022, Laskurain-Iturbe et al., 2021). Additionally, data analytics is extensively employed comprehensively to assess and mitigate their ecological footprints, reinforcing the notion of an industry-wide commitment to environmental preservation and resource conservation, where the focus will be on both digitalisation and sustainable practices. If pharmaceutical 3D printing is to be translated into clinical applications, then it needs to fit within the paradigm of Industry 5.0.
However, the sustainability and environmental impact of pharmaceutical 3D printing is yet to be thoroughly explored. A recent report highlighted that the pharmaceutical sector emits 55 % more carbon emissions than the automotive industry (Belkhir and Elmeligi, 2019, Chen et al., 2023). Hence, the industry may require better monitoring and control over carbon emissions. The purpose of the pharmaceutical industry is to improve human health; however, this should not come at the expense of planetary health. In any case, other sectors have adopted methods to forecast their carbon emission, which in return is influencing their decision making (Elbadawi et al., 2023, Emami Javanmard et al., 2023, Gao et al., 2022, Huang et al., 2022). The practice of forecasting carbon emissions within the pharmaceutical sector will assume a pivotal role in steering decision-making processes. Through the anticipation of forthcoming emissions tied to operational procedures, energy usage, and transportation logistics, the industry will gain the capacity to optimize resource distribution effectively, amplify operational sustainability, uphold regulatory requisites, and bolster conscientious supply chain management. This approach will not only stimulate innovative endeavours but also showcase a commitment to corporate social responsibility, facilitate strategic long-term planning, and mitigate potential hazards, thus aligning the industry with sustainable paradigms and environmentally mindful stewardship.
A study conducted by Elbadawi et al., (2023) investigated the energy consumption of 6 benchtop 3D printers in both standby mode and during the printing process. Standby energy consumption varied between 0.03 and 0.17 kWh, whereas the energy consumption for producing 10 printlets ranged from 0.06 to 3.08 kWh, with printers operating at high temperatures consuming more energy. Carbon emissions ranged from 11.60 to 112.16 g CO2 (eq) per 10 printlets. The study further demonstrated that a reduction in carbon emission can be achieved by reducing the printing operating temperature (Elbadawi et al., 2023).
Building on from the previous study, here the energy consumption of FDM printing was investigated in more detail. Key FDM parameters were explored systematically to determine which are the significant contributors to energy demand. The analysis was performed for 4 dosage forms: tablets, capsules, films and torus. A design of experiment (DoE) was used to explore the research space. The data generated were then used to develop a model that could forecast carbon emissions were and it was subsequently experimentally validated.
Read more here
Hanxiang Li, Manal E. Alkahtani, Abdul W. Basit, Moe Elbadawi, Simon Gaisford, Optimizing environmental sustainability in pharmaceutical 3D printing through machine learning, International Journal of Pharmaceutics, Volume 648, 2023, 123561, ISSN 0378-5173, https://doi.org/10.1016/j.ijpharm.2023.123561.
Read more on Overview of Pharmaceutical 3D printing here:
