Mastering the Softgel Encapsulation Process: A Deep Dive into Precision Manufacturing

Softgel capsules are a cornerstone of modern pharmaceutical and nutraceutical industries, offering consumers a seamless, easy-to-swallow solution that enhances bioavailability and ensures precise dosing. This article will examine the intricate processes involved in softgel encapsulation, highlighting best practices, equipment, and innovations shaping the industry.
Preparing the Essentials: Materials and Facility Requirements
Before encapsulation can commence, the core materials and environmental conditions must be meticulously prepared to ensure a smooth production process.
Gelatin Shell
The softgel shell is the backbone of the capsule, composed primarily of:
- Gelatin: Derived from animal collagen, providing elasticity and strength.
- Plasticizers: Such as glycerin or sorbitol, add flexibility.
- Water: Ensures the gelatin remains workable during the encapsulation process.
- Optional Additives: Opacifiers and colorants may enhance appearance and stability.
The choice of gelatin is crucial, with formulations tailored to meet specific product requirements, including heat resistance, color stability, and compatibility with the fill material.
Fill Material
The fill, often referred to as “the medicine,” may include:
- Oils and Pastes: Common in nutraceuticals like fish oil.
- Suspensions: Containing active pharmaceutical ingredients (APIs) for drug delivery.
- Hydrophilic or Lipophilic Bases: Depending on the solubility of the API.
Each formulation must meet strict viscosity, homogeneity, and stability requirements to prevent issues during encapsulation.
Controlled Environment
Production requires a clean and stable environment:
- Temperature: Maintained around 21°C to keep gelatin pliable.
- Humidity: Production areas typically maintain 25–30% RH, while drying areas are held at 20–25% RH.
- HVAC Systems: Provide air filtration and pressure differentials to ensure cleanliness and prevent cross-contamination.
Operator Expertise: The Cornerstone of Success
Training: A Continuous Investment
Operators of softgel encapsulation machines require rigorous and ongoing training. Compared to other manufacturing roles, becoming proficient in running these machines can take a year or more due to the variability in product formulations and the complexity of the equipment.
The Rotary Die Method: Setting the Industry Standard
The Rotary Die Method is the industry’s gold standard for softgel production. Its seamless forming, filling, and sealing integration in a single operation makes it ideal for high-volume manufacturing.
How It Works
- Gelatin Ribbons: Formed by casting liquid gelatin onto rotating drums, creating thin, uniform sheets.
- Filling: A wedge system injects The fill material between two gelatin ribbons.
- Sealing and Cutting: Rotary dies to cut and seal the capsules simultaneously, forming their final shape.
Key Benefits
- Efficiency: High output with minimal waste.
- Consistency: Ensures uniform capsule size, shape, and fill weight.
- Versatility: Supports a wide range of fill materials and capsule designs.
Essential Equipment for Softgel Encapsulation
Machine Setup
After cleaning, the machine is prepared for production. Key setup steps include:
- Assembling and aligning components such as the dies, Wedge, and timing gears.
- Configuring temperature and speed parameters for the gelatin ribbons and fill material.
- Conducting pre-production checks to ensure the machine is clean, lubricated, and ready for operation.
Softgel production relies on specialized equipment, each tailored to precision and efficiency.
Casting Drums
Gelatin ribbons are cast on rotating drums, where temperature and speed must be precisely controlled to create uniform ribbons. Cooling fans and spreader boxes ensure the ribbons achieve the desired thickness and consistency.
- Create the gelatin ribbons that form the capsule shell.
- Equipped with cooling fans to stabilize ribbon thickness.
- Require smooth, jerk-free rotation to avoid defects.
Rotary Dies
Die rolls determine the size and shape of the capsules. Proper alignment and timing are critical to avoid weak seals or malformed capsules.
- Shape the capsules and ensure uniformity.
- Made from aviation-grade aluminum for durability.
- Require precise alignment for effective sealing.
Wedge (or Segment)
The Wedge is the heart of the encapsulation process, where fill material is injected between the gelatin ribbons as they are sealed into capsules. Wedge temperature varies depending on the shell material, with vegetable-based gelatin requiring higher temperatures (46–57°C) than traditional gelatin (35–45°C).
- Positioned between the dies to inject the fill material.
- Maintains proper temperature to ensure seamless bonding of gelatin ribbons.
- Eliminates air pockets during sealing.
Injection Pump
- Controls the volume of fill material injected into each capsule.
- Operates in sync with the dies to ensure precision.
Lubrication System
Lubricants such as light mineral oil or medium-chain triglycerides (MCT) are applied to reduce sticking and ensure smooth operation. Over-lubrication, however, can extend drying times and affect capsule appearance.
- Applies oils to reduce friction and prevent sticking.
- Ensures consistent operation of the dies and ribbons.

The Encapsulation Process: Step-by-Step
Ribbon Formation
The process begins with gelatin ribbon production:
- Heated gelatin is poured onto casting drums.
- The drums’ rotation creates ribbons of uniform thickness, typically 0.032–0.040 inches.
- Cooling fans stabilize the ribbons before they move to the encapsulation zone.
Filling and Sealing
- Filling: The injection pump delivers a precise amount of material into the gelatin ribbons via the wedge.
- Sealing: Heat and pressure bond the ribbons, forming a seamless capsule.
- Cutting: Rotary dies trim the capsules to their final shape.
Drying
The capsules undergo a two-stage drying process:
- Tumble Drying: Removes most of the moisture.
- Tray Drying: Stabilizes the capsules under controlled airflow and humidity.
Quality Control
Robust quality control systems are integral to softgel production, ensuring product consistency and compliance.
Ribbon Inspection
- Monitored for thickness, transparency, and elasticity.
- Defects such as tears or uneven edges are addressed immediately.
Fill Weight Accuracy
- Verified at regular intervals to ensure proper dosing.
- Adjustments are made promptly to maintain consistency.
Sealing Integrity
- Burst tests and visual inspections confirm the strength and uniformity of seams.
- Capsules are examined for leaks or weak points.
Final Testing
Capsules are evaluated for:
- Appearance: Color, size, and shape.
- Stability: Ensures long-term efficacy and safety.
- Dissolution and Disintegration: Verify performance in the body.

Innovations Driving the Industry Forward
Plant-Based Gelatin
- Responds to growing demand for vegan, halal, and kosher products.
- Offers similar properties to traditional gelatin.
Advanced Coatings
- Enable enteric and delayed-release coating functionalities.
- Enhance bioavailability for challenging APIs.
Common Problems Encountered & Solutions
Softgel encapsulation is a complex process that presents various challenges. Below are some common issues and practical solutions to address them:
1. Uneven Ribbon Thickness
Problem: Inconsistent gelatin ribbon thickness can lead to improper sealing or capsule defects.
Solution:
- Regularly calibrate casting drums and monitor temperature and drum speed.
- Use micrometers to measure ribbon thickness periodically during production.
- Ensure cooling fans and spreader boxes are functioning optimally to maintain uniformity.
2. Weak Seams or Leaks
Problem: Poorly sealed capsules may burst or fail quality checks.
Solution:
- Adjust the Wedge temperature and ensure proper alignment of rotary dies.
- Monitor seam thickness to ensure it meets 20% of the ribbon thickness.
- Conduct frequent burst tests to catch and resolve issues early.
3. Fill Weight Variability
Problem: Inconsistent dosing can compromise product efficacy and safety.
Solution:
- Perform routine checks on injection pumps and calibrate them for accurate fill volume.
- Use servo-controlled pumps to maintain precise timing and injection rates.
- Regularly inspect and replace worn-out pump components.
4. Capsule Sticking
Problem: Capsules sticking to each other or machine components disrupt production and drying.
Solution:
- Use appropriate lubricants on ribbons and Wedges, such as light mineral or MCT.
- Avoid over-lubrication, which can prolong drying times.
- Ensure proper airflow in drying baskets and maintain optimal humidity levels.
5. Gelatin Scrap Management
Problem: Excessive scrap gelatin increases waste and production costs.
Solution:
- Implement recycling practices, such as solvent washing or repurposing for non-pharmaceutical use.
- Optimize die alignment and minimize over-trimming to reduce scrap generation.
Expert Insights
Developing a successful soft gelatin capsule manufacturer process requires collaboration between formulation scientists, quality assurance experts, and manufacturing engineers.
The art of softgel encapsulation combines the best of material science,
engineering, and human expertise.”
Vitor Antraco
“Achieving excellence in softgel manufacturing demands a commitment
to continuous improvement and adaptability.”
Sair Torregrosa
Conclusion
Softgel encapsulation merges art and science, requiring precision, expertise, and continuous improvement to produce high-quality products. Each step is optimized for efficiency and quality, from the careful casting of gelatin ribbons to the precise injection of fill materials. Understanding these processes can inspire innovation and enhance production outcomes for professionals in the pharmaceutical and nutraceutical industries. Whether you’re a manufacturer, supplier, or industry enthusiast, the world of softgel encapsulation offers endless opportunities for exploration and innovation.
Read the original text here
Source: Vitor Jacó Antraco and Sair Torregrosa, LinkedIn Mastering the Softgel Encapsulation Process: A Deep Dive into Precision Manufacturing
See the full article series dedicated to softgel capsules:
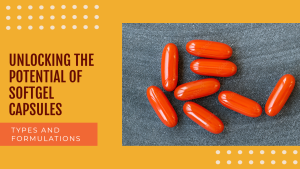
- Optimizing Softgel Fill Formulation: Key Considerations
- The Ultimate Guide to Soft Gelatin Capsule Manufacturing


