Discover Omya’s state of the art pharmaceutical laboratory here!
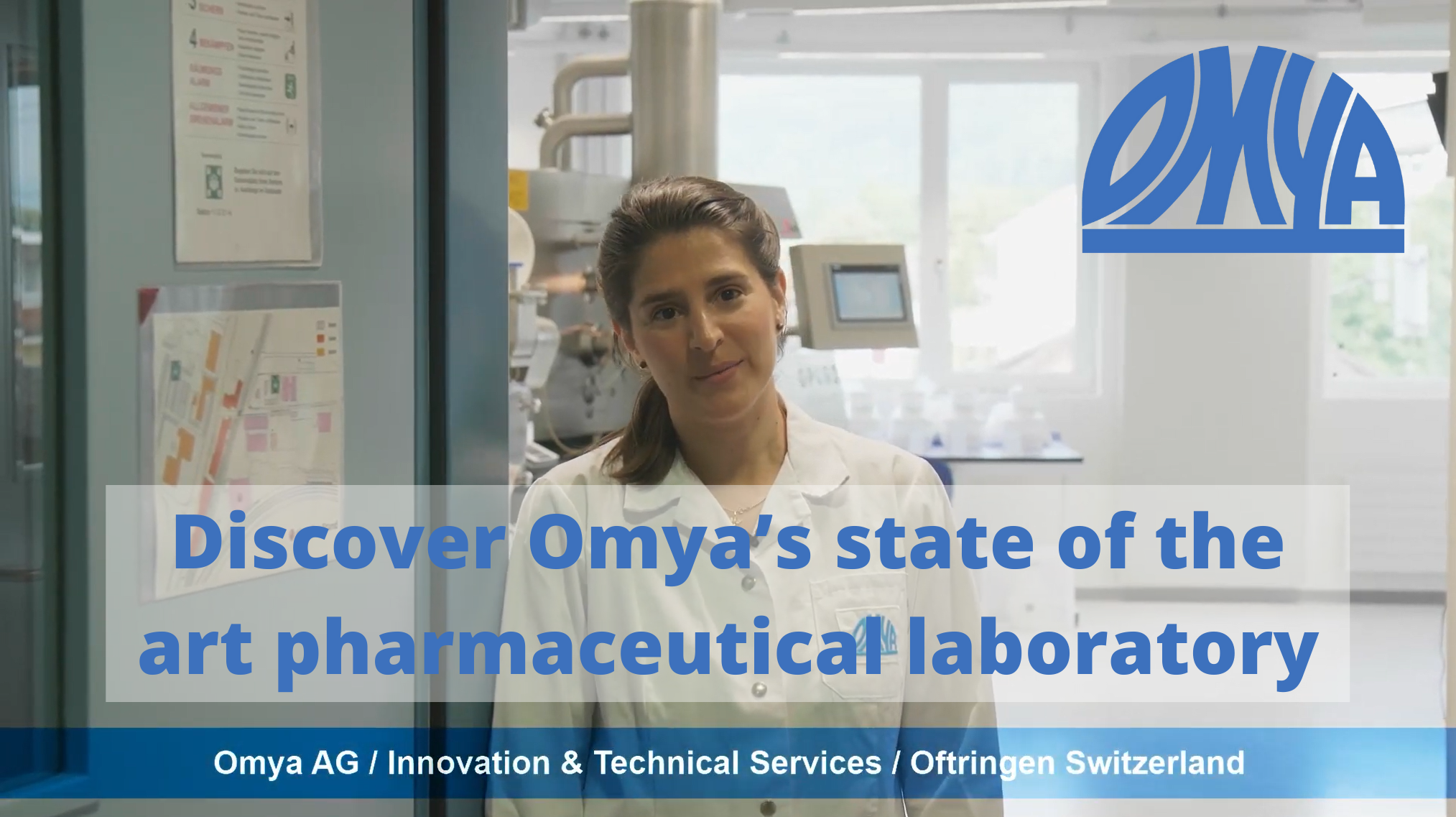
Omya continues to build on its mineral expertise with extensive research & development. New facilities and equipment show their commitment to innovation. Their team of pharma experts is working on new tailor-made functional mineral solutions for specific applications, striving to continuously optimize existing products to meet the changing needs of the industry. Find all Omya products here!
Discover Omya’s state of the art pharmaceutical laboratory, explained by Carolina Diaz Quijano Reichert:
Transcript: Welcome to Omya Pharmaceutical Application Lab!
We have been working in this lab since 2016. Come on in. This lab is divided in different sections. We have our manufacturing, our parameters measurement section. The manufacturing section is divided in granulation and tableting facilities.
Our granulation facilities start with the roller compaction. This is our Fitzpatrick Equipment, lab size equipment for dry granulation. So dry granulation facility has the advantages of being a continuous process. It is a dry process, so it doesn’t affect actives that are sensitive to moisture. And this machine operates by feeding the powders through the feeding system here. There will be two screws that will push the powder into the compaction area, where we have two roles that will compact the powder into a band that will be later on milled and sieved in this section of the equipment.
This type of process the dry granulation can use binders or in the case of our own omya pharm 500 OG. There is no need for binder because we have a structure that is a lamellar that will interlocked and generate mechanical bonding that will be creating granules that are stable enough. And there is no need for a polymeric binder. It is really our star granulation facility.
This is our wet granulation facility. This is our GPC G2, by Glatt, a fluidized bed. Wet granulation processes have a few disadvantages compared to dry granulation processes, as we were seeing before, because they are done in batch in general and also they have moisture. So if there is an active sensitivity, this could cause some issues. But on the other hand, they generate granules that are much fluffier, they have less density and therefore they are better for, for example, chewable tablets. In this case, actually, we are manufacturing here granules that will go for direct compression into orange chewable antiacids.
This equipment is very good in terms of versatility. It allows us to load particles, agglomerate them and also encapsulate them and coat them. In terms of measuring parameters of granules, we have, for example, here the RWK Granutest. This facility can measure flow of granules and allows us to tell to predict how good these granules will flow in a hopper in a tableting machine.
We can test here and not only flow through an orifice, but also the angle of repose. We have other facilities, granulation facilities that are new to our lab. We have, for example, the Glatt high shear mixer, and we have, for example, the hot melt extrusion by Dr. Collin. Here you can see the Glatt equipment and the Dr. Collin equipment. The real star of this lab is our tabletting machine.
The Fette compacting 1200i. This machine is a production scale, small production scale, machine, and it allow us on certain customization to work in the same conditions that our customers do. This machine has been customized to be able to work with small quantities. Normally, the Fette 1200i has 16 stations and it can produce quarter million tablets per hour. We have reduced the speed to thirty thousand tablets per hour, which is a good speed to show reproducibility at the customer. But at the same time, it allows us to work with small quantities of material, particularly APIs.
The customization we have done, we have reduce the amount of punches from 16 to eight. We have double tooling. We have gravitational feeding instead of an automatic feeding. Yeah, that’s mainly the customization we have done to this machine.
So we have the filling station here. Then we have the pre compression station, then we have in the back the compression station and the ejection where tablets are ejected. So as you can see, this is the main feature of our tabletting equipment that we can really reproduce the parameters that will be used at our customer site.
We can also measure parameters in this lab. For example, we can make desintegration of tablets. In this case, for example, we have the Disitest 50 from Pharmatron to measure desintegration, but we can also measure hardness and friability of tablets. Hardness can be measured by the Multitest 50 from Pharmatron and friability by the RWK equipment.
The last parameter measurement equipment that I want to show you is this Sotax. The Sotax can measure dissolution so we can study kinetics of drug release. The Sotax equipment can measure the release of actives in different medias. In this case, we are measuring caffeine release from orally dispersible tablets. We can see how fast the dissolution of the caffeine is in the media. We hope you have enjoyed the tour to Omya pharmaceutical lab facilities. Thank you for your visit and we look forward to working with you. Bye.