Calcium carbonate as a replacement for titanium dioxide in coating: the importance of particle engineering
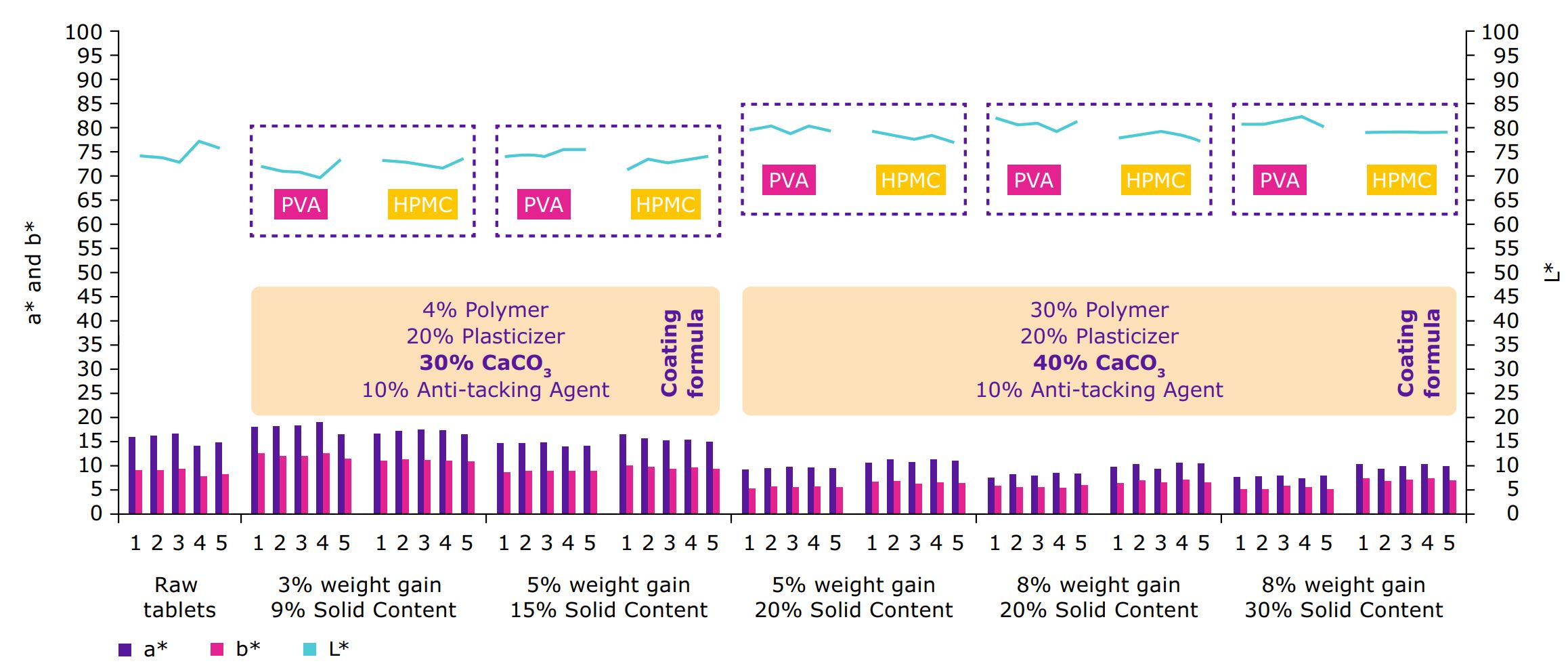
Uniform colored and white coatings applied to tablets create a homogeneous appearance across batches, improving aesthetics and patient compliance. Titanium dioxide is used extensively in solid dosage forms for this purpose, serving as an opacifier and colorant. Due to its high refractive index, it provides highest opacity and coverage for a coating.
Based on a safety assessment of titanium dioxide (E171) by the European Food Safety Authority (EFSA)1 regarding concerns about potential genotoxic effects, the EU Commission has withdrawn the authorization to use titanium dioxide in foods and dietary supplements. The ban of titanium dioxide became effective in August 2022 based on the Commission Regulation (EU) 2022/63 and its removal from pharmaceutical products in the EU is now being considered.2 A possible ban would have a major impact as it is estimated that 91,000 human medicinal products contain titanium dioxide.3
Given these regulatory trends, there is a need to identify sustainable replacements for titanium dioxide. With the current approval status as the only other white drug colorant in the EU, calcium carbonate is seen as the most likely alternative. Parteck® TA excipient – a calcium carbonate with a defined morphology and particle size distribution – by Merck has been developed for use in tablet film coatings and addresses the need for both good opacity and process efficiency.
This white paper highlights how particle engineering supports an optimal performance of calcium carbonate in coating applications, comparing Parteck® TA excipient to the industry benchmark titanium dioxide.
Physical Properties and Characterization
Selection of a suitable grade of calcium carbonate for coating formulations requires detailed understanding of the role particle morphology and particle design play in the development process.
The opacity of white pigments is largely due to their ability to scatter incident light. Scattering depends on several factors including the optical properties of the particles and their particle size, shape, surface structure, spatial orientation, and particle arrangement.4

In this study, Parteck® TA calcium carbonate was characterized by scanning electron microscopy (SEM) and powder x-ray diffraction (PXRD). The particle engineered product provides a unique particle morphology as demonstrated in the SEM images (Figure 1).
Its specific pattern in the diffractogram corresponds to the morphology of calcite with rhombohedral structure and frequent hexagonal crystals as confirmed by PXRD measurements (Figure 2).


Good coverage of tablet cores can be achieved by an optimized range of the particle size distribution (PSD, Figure 3 and Table 1); a reduction of the particle size to a certain extent can increase the light scattering properties and thus the opacity of the particles.4 As an additional benefit, a defined PSD can ensure a consistent performance and minimize batch-to-batch variation.
Table 1.
Particle sizes and BET specific surface areas of Parteck® TA excipient vs. other market samples (C1–C4). Particle size measured using laser diffraction; particle surface measured according to BET (Brunauer, Emmett and Teller) using nitrogen adsorption method.
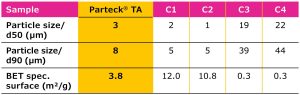
Pre-screening with drawdown cards
To streamline the film coating development process and formulation design, dedicated screening methods can be used. Film casting on defined color cards allows rapid assessment of opacity at small scale without the necessity of coating trials. The opacity equates to the hiding power of a pigment, whereas the opacity degree of a film is defined by the ratio of the reflectance of the incident light on a black and a white background. In the case of a complete coverage of the black color card, the opacity is 100%.
Figure 4 shows results of a pre-screening step, conducted with films drawn on black and white cards. In comparison to titanium dioxide containing films, a similar coverage could be achieved with Parteck® TA excipient by using higher concentrations.
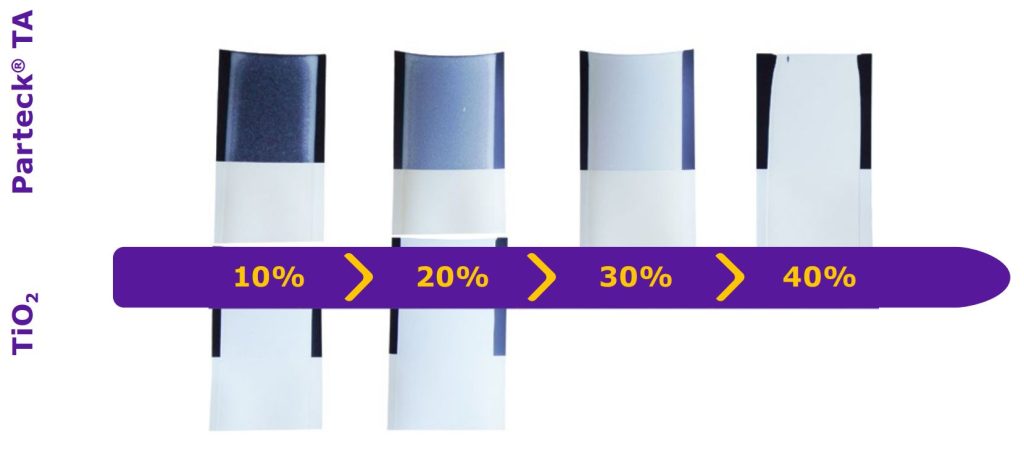
Basis formulation: Parteck® COAT solution (20%)
Thickness of the film: 0.08–0.15 mm
Card film applicator: Moeller, CI-K3-125-M
Application in tablet film coatings
For the simulation of colored drug substances, core tablets were manufactured with a content of 0.5% red iron oxide. This approach mimics a challenging scenario presented by strong colored, heterogeneously distributed drug substance within the tablet core. The coating processes were performed in a rotating drum
coater type LDCS (Vector Freund Corporation). For the
comparative study, it was the purpose to investigate the coverage of the film coatings, the distribution on the tablet surface and galenical properties of the coated tablets.
Tablet cores:
Standard formulation: 98% mannitol, 1.5% magnesium stearate, 0.5% red iron oxide
Red iron oxide: Used to demonstrate the opacity performance
Convex tablets: 500 mg weight, 11 mm diameter; tabletting performed with tablet press Fette 1200i (Fette Compacting GmbH)Coating suspension:
10% talcum, 20% triethyl citrate; the amount of HPMC and Parteck® COAT (PVA) was adapted to the individual formulations
Coverage of the film coatings
Enhanced coverage of the core tablets can be achieved
by an increased tablet weight gain (Figure 5). A weight
gain of 5–8% was typically sufficient to cover most of
the strongly colored drug substance. A loading limit
of up to 20% tablet weight gain was evaluated for
information purposes.

Distribution on tablet surface
SEM photos of the surface and the cut of the tablet show a homogeneous distribution of the calcium carbonate particles in the coating (Figure 6) and over the entire coating area.

Galenical properties
According to the study results the galenical properties of tablets with Parteck® TA calcium carbonate (5% weight
gain) were similar to the tablets with titanium dioxide (5% weight gain). No impact on friability or tablet hardness
was observed (Table 2).

Download the the full White Paper on “Calcium carbonate as a replacement for titanium dioxide in coating: the importance of particle engineering” here
(click the picture to download the White Paper)
Source: Merck White Paper “Calcium carbonate as a replacement for titanium dioxide in coating: the importance of particle engineering”
Do you need more information or a sample of excipients by Merck?