Spray Drying for Direct Compression of Pharmaceuticals
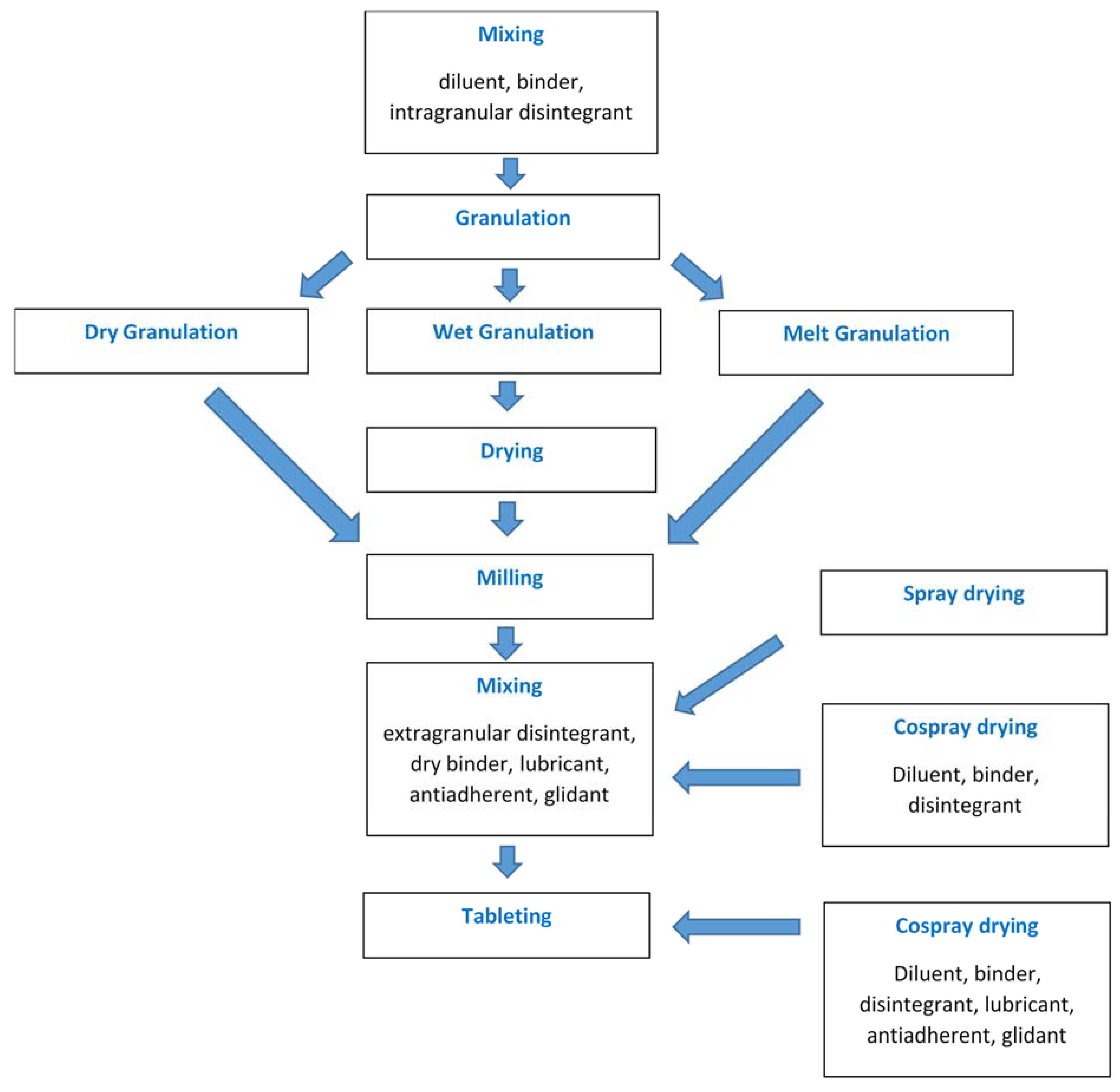
Tableting by direct compression (DC) is one of the simplest and most cost-effective drug manufacturing approaches. However, most active pharmaceutical ingredients (APIs) and excipients lack the compression and flow properties required to meet the needs of high-speed industrial tablet presses.
Therefore, the majority of DC APIs and excipients are modified via processing/co-processing particle engineering techniques to boost their properties. Spray drying is one of the most commonly employed techniques to prepare DC grades of APIs and excipients with prominent advantages. This review aims to present an overview of the commercially marketed and investigationally-prepared DC APIs and excipients produced by spray drying.
Download the full publication here: Spray Drying for Direct Compression of Pharmaceuticals
or continue reading here: Al-Zoubi, N.; Gharaibeh, S.; Aljaberi, A.; Nikolakakis, I. Spray Drying for Direct Compression of Pharmaceuticals. Processes 2021, 9, 267. https://doi.org/10.3390/pr9020267
Interesting Overview on Excipients in this publication up from Chapter 5:
5. Direct-Compression Spray-Dried Excipients
5.1. Spray-Dried Lactose
The first commercially available spray-dried excipient for direct compression was lactose, introduced in 1956 [50]. Spray drying resulted in a final product that comprised 80–90% of α-lactose monohydrate crystalline particles agglomerated into spherical units with the aid of the remaining amorphous material. The amorphous component was produced from the dissolved lactose in the feed slurry. Spray-dried lactose would usually contain 9–12% β-lactose, predominantly in the amorphous matrix [51]. The spray-dried agglomerates exhibited enhanced flowability and compressibility compared to either 100% amorphous or crystalline α-lactose monohydrate. The excellent flow resulted from the large particle size and spherical shape of the agglomerates. On the other hand, the amorphous fraction present contributed to superior compressibility by virtue of higher degree of plastic deformation and better binding [52]. In theory, compaction of the spray-dried lactose combines fragmentation and plastic deformation of the crystalline monohydrate and the amorphous fractions, respectively [50,53]. However, the consolidation mechanism of lactose also depends on its particle size. The brittle-ductile transition diameter of lactose is 45 µm, but when the particle size is less than that, plastic deformation may be the main consolidation mechanism of spray-dried lactose [51].
The direct compression characteristics of the initial spray-dried lactose were improved over the years by optimizing mainly two factors: the percentage of amorphous content and the primary particle size of α-lactose monohydrate spray-dried particles [54,55]. For example, optimization of the amorphous content is claimed to explain the better compactability of the FlowLac® 90 grade compared with the regular spray-dried FlowLac® 100 [56].
Different grades of spray-dried lactose are commercially available differing in tableting performance and sensitivity to environmental moisture during storage. In this context, Pharmatose® DCL 14, an improved spray-dried lactose grade produced from smaller primary particles of α-lactose monohydrate, was compared to the regular spray-dried lactose grade Pharmatose® DCL 11. Both grades showed similar flow but different compaction behavior. Pharmatose® DCL 14 was significantly more compactible, which was attributed to the greater total surface area provided by the smaller primary particles [51]. The compactability of Pharmatose® DCL 14 was preserved after storage of the tablets at either 58% or 33% RH for 21 days compared to initial tablets. Interestingly, the strength of Pharmatose® DCL 11 tablets increased after exposure to the high RH conditions for the same period. Re-crystallization of the amorphous content in the tablets and bridge formation was considered the reason for the increase in tablet strength. Conversely, pre-exposure of the powder to moisture before compression reduced the compactability of both grades, which was ascribed to the conversion of amorphous content to crystalline before compression [57]. Finally, although it cannot be generalized, regular grades from different manufacturers appear to have similar qualities. For example, the regular spray-dried grades of lactose FlowLac® 100 and Pharmatose® DCL 11 were found to exhibit similar flowability, compressibility and compactability behavior [58].
Microcrystalline cellulose (MCC) is another widely used spray-dried excipient. Although it can be synthesized by different processes, mineral acid hydrolysis is the method of choice to produce pure α-cellulose. First, cellulose is partially depolymerized and at a next step it is neutralized and spray-dried [59,60]. The final product is a white, tasteless, and odorless powder. Different grades of various particle size distributions and moisture contents are available, which can be produced by controlling the agglomeration through manipulation of the spray-drying conditions.
Moreover, specific cellulose pulps enabled the manufacturing of MCC grades that exhibit high bulk density [61]. Some of the commercially available products are Avicel®, Vivapur®, and Emcocel®. For additional information regarding the preparation of various MCC grades and their properties and applications, the reader is referred to a recent book chapter by Chaerunisaa et al. [62] and an extensive review by Thoorens et al. [61].
5.3. Spray-Dried Calcium Salts
Three different calcium salts were developed as granular materials by spray drying to improve their compaction and flow properties. The first is calcium lactate pentahydrate (Puracal® DC), a brittle crystalline material that exhibits low compaction-speed sensitivity. However, it has low fragmentation tendency, which makes it a lubricant-sensitive filler [63]. Disintegration and dissolution of prototype tablet formulations using calcium lactate pentahydrate alone or with MCC were fast and complete [63]. Next calcium salt excipient is spray-dried anhydrous dicalcium phosphate (Fujicalin®). Its properties were thoroughly investigated and compared to the corresponding regular anhydrous dicalcium phosphate; it has smaller particle size with higher specific surface area, porosity and compactability, but similar flowability [64,65]. Due to its high brittleness, Fujicalin® exhibited stability against over-lubrication with magnesium stearate, which was demonstrated for different mixers and mixing times [66]. The third calcium-salt-based excipient is spray-dried tricalcium phosphate (Tri-Cafos® 500. It has a spongy structure and, thus, a large specific surface area. Unlike the other directly compressible calcium salts, it consolidates primarily by plastic deformation. When used as a co-diluent, it results in increased porosity and faster tablet disintegration [67].
5.4. Spray-Dried Sugars and Polyols
Spray-dried sugars and polyols are gaining increased attention as fillers in chewable, suckable, effervescent and orally disintegrating tablets. Examples include sucrose (Compressuc® PS), maltose (Advantose® 100), mannitol (Parteck® M, Pearlitol® SD, and Mannogem®), and sorbitol (Neosorb® XTAB, Parteck® SI). Among these, mannitol has a range of interesting properties that have made it one of the most used fillers for the aforementioned tablet forms [68]. Besides sweetness, it has a negative heat of solution releasing a cooling sensation to the mouth. Also, it is not hygroscopic, although very soluble in water, thus offering excellent stability and compatibility with drugs [69]. Spray-dried mannitol is commercially available in two grades: the 100 or EZ and 200 or XL with the former having smaller mean particle size [70]. Unlike lactose, spray drying does not affect its crystallinity with the final product being comprised of β crystals (Parteck®) or a mixture of α and β mannitol crystals (Pearlitol®, and Mannogem®) [71,72]. Recently, the powder and tablet properties of several brands and grades of spray-dried mannitol were compared with commercially available granulated grades [70,72]. Except for a minor increase in the disintegration time observed after one-week storage (25 °C/75% RH), the tablets of spray-dried mannitol grades showed superior physical stability over the granulation-based grades.
Neosorb® XTAB is a powdered form of sorbitol developed by Roquette as a tooth-friendly filler to make sugar-free tablets [73]. Sorbitol instant (Parteck® SI, Merck) is a spray-dried free-flowing low-hygroscopicity crystalline grade of sorbitol with improved compressibility and high adsorption capacity for the preparation of ordered mixtures due to its loosely packed, randomly oriented, interwoven filamentary crystals [74]. Advantose® 100 is a nonhygroscopic free-flowing directly-compressible powder form of the disaccharide maltose. Despite its crystalline nature and fragmentation during consolidation, its compactability has been shown to be affected by lubricants over a range of compression forces [75]. Compressuc® PS is a spray-dried sucrose grade that complies with the monograph “sucrose” of the USP/NF and Ph. Eur. [76].
5.5. Spray-Dried Rice Starch
Era-tab® and Primotab ET® are excipients based on agglomerated rice starch particles that were used to be commercially available spray-dried grades. The usefulness of spray-dried rice starch for direct compression was evaluated against several fillers in terms of physical properties and tabletability. Era-tab® was shown to possess excellent flowability, compactability as well as disintegration and dissolution properties. From its drawbacks, the most important are its moderate dilution potential and lubricant sensitivity [77,78]. However, the latter is lower when compared to other starch products, and it is considered sufficient for tablet formulations [79].
In addition to studies on commercialized spray-dried excipients, investigation of the effect of spray drying process on the mechanical properties and reworkability of some known polymers has been reported. The main research studies on investigational spray-dried alone or co-spray dried excipients are summarized in Table 2. Spray-dried hypromellose acetate succinate (HPMCAS) from organic solutions exhibited higher hardness and lower out-of-die yield strength [80], but higher tensile strength of compacts than unprocessed material, indicating improved ability to form strong compacts upon loading [49,80].
Rege et al. [81,82] spray-dried chitinosans that had undergone N- deacetylation and depolymerization. As compared to the tray-dried product, spray-dried chitinosan particles were more isodiametric and exhibited better flowability. Moreover, the compaction properties of their mixture with tetracycline, used as a model drug, were superior.
Kolakovic et al. investigated the physical and mechanical properties of spray-dried cellulose nanofibers compared to two commercial grades of MCC, Avicel® PH101 and Avicel® PH102. The results showed that spray-dried nanofibrillated cellulose has a better flowability than Avicel® PH101 and its addition to Avicel® PH102 improved the flowability of the resulting mixtures. Tablets with a model drug (paracetamol) were successfully prepared on an eccentric press. However, compared to microcrystalline cellulose, spray dried nanofibrillated cellulose was more brittle but less deformable and compactable [83].
The results of the above studies show that spray drying decreased the compressibility but increased the brittleness of carbohydrate-based excipients. Since the outcome of compaction also depends on the initial stage of particle rearrangement before compact formation, and since the spray-dried particles achieve more uniform packing and easier particle rearrangement, the overall effect of spray drying on tabletability should be balanced considering the individual effects on flowability and compression behavior.
6. Direct-Compression Co-Spray Dried Excipients
6.1. Lactose-Based
6.1.1. Lactose-Cellulose (Cellactose®)
Cellactose® 80 is composed of 75% α-Lactose monohydrate and 25% cellulose powder (3:1 ratio) co-spray dried mixture. Its reported angle of repose is 34°, the bulk density 0.37 g/cm3 and the tapped density 0.49 g/cm3 [84]. According to the manufacturer [84], it is designed as an excipient for manufacturing tablets by direct compression due to its superior flowability, reduced segregation tendency and compressibility. Casalderrey et al. [85] compared the properties of a 3:1 ratio of α-Lactose monohydrate/microcrystalline cellulose combination processed either by dry granulation or extrusion/spheronization with those of Cellactose® powder of similar particle size. Cellactose® showed better sphericity and flowability than the dry granulation blend (Carr’s index 24% compared with 37%). Additionally, Cellactose® had improved mechanical properties, but much poorer disintegration than tablets of the other blends compressed at the same high punch pressure. The strength and water-resistance of well-compacted Cellactose® tablets were attributed to the spatial distribution of cellulose and lactose in Cellactose® particles, rather than to β-lactose content or extra-particular structural features [85]. Arida and Al-Tabakha [86] reported superior compactability of Cellactose® over the counterpart physical mixture.
6.1.2. Lactose–MCC (MicroceLac® 100)
MicroceLac® 100 is a co-spray dried mixture of 75% α-Lactose monohydrate and 25% microcrystalline cellulose [87]. According to the product’s brochure (MEGGLE’s co-processed lactose grades for direct compression: MicroceLac® 100), it has a Carr’s index of 21%, angle of repose equal to 34° and a bulk density of 0.46 g/cm3 and it is claimed to have good flowability and compaction properties, thus making it suitable for direct compression. Compared to its counterpart physical mixture, MicroceLac® 100 showed better flowability and tablet mechanical strength [88,89], faster disintegration and drug dissolution (f2 = 16.61) [89]. However, it was more susceptible to water-induced crystallization due to thermodynamic instability and crystallization of the amorphous content into stable crystalline form [88]. The Heckel yield pressure of MicroceLac® 100 (170 MPa) was very similar to that of spray-dried lactose, FlowLac® 100 (168 MPa), indicating similar deformability [90].
6.1.3. Lactose-Starch (StarLac®)
StarLac® is a co-spray dried material composed of 85% α-lactose monohydrate and 15% white maize starch manufactured by Meggle Pharma. According to the manufacturer, its Carr’s index is 19.4% and the angle of repose is 29° [91]. The lower Carr’s index compared to Cellactose® and MicroceLac® 100 may be attributed to higher sphericity and smoother surface of particles (Figure 5). The reported Heckel yield pressure is lower for StarLac® than FlowLac® indicating higher plasticity [90,92]. Hauschild and Picker investigated the tableting properties of StarLac® and compared it with FlowLac® (spray-dried lactose) and a corresponding physical mixture of FlowLac® and maize starch. They concluded that StarLac® has good compactability and similar compression properties to FlowLac®. Moreover, the high deformability of StarLac® makes it an interesting excipient for use in the tableting of pressure-sensitive drugs [93].
6.1.4. Lactose-MCC-Starch (CombiLac®)
CombiLac® is composed of 70% α-lactose monohydrate, 20% microcrystalline cellulose, and 10% white native corn starch [94]. Mužíková et al. [95] studied the properties of this spray-dried ternary mixture. They compared the flowability, compactability, and tablet properties of CombiLac® with the corresponding physical mixture. They found that CombiLac® had lower Hausner’s ratio, indicating better packing and flowability, and better tabletability than the physical mixture. Moreover, the compaction of CombiLac® was more sensitive to the presence of lubricants in the formulation, which is explained by the lower fragmentation propensity of the brittle main excipient (lactose) when co-spray dried with the plastic co-excipients (starch and MCC) compared to the corresponding physical mixture. Bowles et al. [96] characterized the tableting behavior for a range of co-processed excipients. Their results revealed that CombiLac® had lower Carr’s index, better ejectability, slightly faster compact disintegration (<60 s) but similar compressibility, compactability and tabletability profiles compared to MicroceLac® 100.
6.2. MCC-Based
6.2.1. MCC–Mannitol (Avicel® HFE)
Microcrystalline cellulose-Mannitol (Avicel® HFE) is a co-spray dried material composed of 90% microcrystalline cellulose and 10% mannitol [98]. Avicel® HFE-102 is reported to have a nominal particle size of 100 µm, angle of repose of 30.67°, bulk density around 0.41 g/cm3 and Carr’s index of 19.19% [98,99]. It showed similar compression behavior and slightly faster disintegration of compacts compared to Avicel® PH-102 [90,96]. Moreover, tablets compressed at a pressure of 78 MPa were strong with tensile strength between 5 and 6 MPa, friability 0.01% and disintegration time 4.03 min [99]. This mannitol/microcrystalline cellulose combination improves palatability and decreases the disintegration time due to the good water solubility, wetting properties, and negative heat of solution of mannitol [100]. Therefore, this co-processed material is suitable for direct compression of chewable tablets.
6.2.2. MCC–Guar Gum (Avicel® CE-15)
Microcrystalline cellulose-guar gum (Avicel® CE-15) is a co-spray dried material composed of 85% microcrystalline cellulose and 15% guar gum [98,99]. It has Carr’s index 19.46%, indicating intermediate flowability [99]. Avicel® CE-15 is reported to have a D90 of 221.06 µm, a specific surface area of 0.5 m2/g, and a moisture content of 4.66% [99]. It has also been reported that tablets compressed at 130 MPa had friability 0.58%, disintegration time 7.27 min, and tensile strength around 2 MPa. Therefore, it is suitable for direct compression operations, especially for chewable tablets due to guar gum, which provides a suitable sensory experience by reducing the grittiness of MCC.
6.2.3. MCC–Dicalcium Phosphate (Avicel® DG)
Avicel® DG is a co-spray dried material composed of 75% microcrystalline cellulose and 25% anhydrous dibasic calcium phosphate. It is proposed by the manufacturer for the tableting of difficult to compress materials and for dry granulation [98]. The combination of plastic and brittle material decreases bonding during roller compaction, facilitating breakage into granules. Subsequently, during tableting, both the high amount of small particles of the inorganic excipient and the plastically deforming microcrystalline cellulose particle surfaces provide sufficient surface area for bonding and compact formation [99]. Avicel® DG has been investigated for DC tableting, and its tablets showed rapid disintegration, high tensile strength, and low friability. However, it has suboptimal flowability with relatively high Carr’s index (24.98%) [99].
6.2.4. Silicified Microcrystalline Cellulose
Silicified microcrystalline cellulose (MCC) grades Prosolv® SMCC and Avicel® SMCC are co-spray dried materials composed of 98% microcrystalline cellulose and 2% colloidal silicon dioxide (CSD) [1,98,101]. Five grades of Prosolv® SMCC (50, 50 LD, 90, HD 90 and 90 LM) and three grades of Avicel® SMCC (50, 90, and HD 90) are available commercially that differ in particle size and bulk density. Silicified MCC has shown better flowability [102] and reduced stickiness [103] compared to non-silicified grades. In addition, it has been reported that compacts of Prosolv® SMCC 90 and Prosolv® SMCC 90 HD had disintegration time below 1 min at compression forces of 3, 3.5, and 4 KN [104]. The compaction behavior of Prosolv® SMCC 90 was studied and compared to MCC [105]. Both excipients showed similar densification behavior for compression pressures up to 400 MPa. In addition, it was found that the post-compaction relaxation of the corresponding tablets was also similar. However, the presence of lubricant (magnesium stearate) affected the relaxation of SMCC 90 tablets which was ascribed to a small negative effect of CSD on the interparticle bonding strength of unlubricated MCC. The mechanical strength of the tablets of the two excipients was similar at compaction pressures up to 400 MPa. Mixing with lubricant decreased the strength for both types of tablets, and the effect was more pronounced in the case of MCC [105]. Kachrimanis et al. [106] confirmed that there is a slight increase in tablet strength but a marked increase in the disintegration time of Prosolv® compared to Avicel® tablets for solid fractions between 0.7 and 0.9, which is similar to the range of pharmaceutical tablets. They also suggested that SiO2 acts as a barrier or sink of moisture for RH up to 52%, but at RH 72% the interparticle spaces become saturated with moisture, thus not allowing water permeation into MCC which cannot act as disintegrant resulting in higher disintegration times.
In 2010, JRS PHARMA introduced Prosolv® EASYtab as an excipient that fulfills several desired features for direct compression purposes [107]. It can be simply mixed with granules or DC grades of active ingredients to form an RTC mixture [108], but extra disintegrant has to be added for products containing high content of solid dispersions in order to shorten the disintegration time [109]. Aljaberi et al. [110] compared the compaction and dissolution performance of Prosolv® EASYtab with corresponding physical mixtures of MCC or SMCC with complementary excipients (colloidal silicon dioxide, sodium starch glycolate, and sodium stearyl fumarate). Prosolv® EASYtab exhibited comparable compactability, dissolution and stability with the corresponding MCC or Prosolv® SMCC physical mixtures.
6.3. Starch-Based
StarCap1500®
StarCap1500® is a co-spray dried material composed of 90% corn starch and 10% pregelatinized starch [1]. Mužíková and Eimerová [111] investigated the compaction energies, mechanical strength and disintegration time of StarCap1500® compacts. They found that they had higher tensile strength than Starch1500® of the same size compressed under the same conditions. However, the compact strength of StarCap 1500® was prominently reduced when mixed with 0.4% magnesium stearate, which should be ascribed to the low fragmentation tendency since starch is elastoplastic. Additionally, researchers found that StarCap 1500® tablets had significantly shorter disintegration time compared to Starch®1500 which was attributed to a more efficient capillary network. The total compaction work expended was significantly larger and the decompression work lower for StarCap 1500® than Starch®1500 attributed to the lower elastic relaxation of StarCap 1500® [111].
6.4. Sugar-Based
6.4.1. Glucose-Dextrates (Emdex®)
Glucose monohydrate—Dextrates, NF (Emdex®) is manufactured by JRS PHARMA. According to the manufacturer [112], this co-spray dried material comprises 95% glucose monohydrate and 5% oligosaccharides derived from starch (Dextrates, NF). It has an average particle size of 200 µm and offers several benefits as a water-soluble filler/binder in direct compression formulations. It has excellent packing and flow properties with Hausner’s ratio of 1.07 and angle of repose of 30°. Additionally, compression of Emdex® at forces between 3 kN and 15 kN produced tablets with tensile strength between 0.3 MPa and 2.5 MPa. These features, besides a pleasant sweet taste, make it suitable for direct compression of chewable, effervescent, and ingestible tablet formulations processed at compression forces greater than about 10 kN [112].
6.4.2. Fructose–Starch (Advantose® FS95)
Fructose-starch co-spray dried (Advantose® FS95) is manufactured by SPI Pharma. Despite the poor compressibility of fructose, when it is co-spray dried with a small amount of starch (5%), the combination product becomes directly compressible [113]. Moreover, Advantose® FS95 has a lower hygroscopicity and a particle size distribution that ensures good flow properties with an angle of repose of 12°. Besides the excellent compressibility profile, it has reduced friability. Due to its sweetness, it is recommended for use in children’s chewable multi-vitamin tablets [113].
6.4.3. Sucrose–Maltodextrin–Invert Sugar
Compressuc® MS is a co-spray dried product composed of sucrose, maltodextrin (2.3% ± 0.5%) and invert sugar (1.7% max) with a porous particle structure. It complies with the USP-NF under the monograph “Compressible sugar”. It has a mean diameter between 150 and 300 µm, bulk density between 0.53 and 0.61 g/cm3 and tapped density between 0.61 and 0.71 g/cm3. As it is the case with the spray-dried sucrose grade (Compressuc® PS), Compressuc® MS is particularly suitable for the production of chewable and effervescent tablets [76].
6.5. Inorganic-Based
CS90 and MS90 are co-spray dried filler-binder marketed by SPI Pharma. CS90 is composed of 90% calcium carbonate and 10% starch with a typical median particle size of 150–175 µm and tapped density of 0.85 g/cm3. MS90 comprises 95% magnesium hydroxide and 5% starch with similar particle size distribution and density to CS 90. Both excipients are recommended for the manufacture of antacid chewable and mineral supplement tablets. Due to the similarity in their physical properties, they can be easily mixed and combined to prepare antacid tablets [114,115].
6.6. Investigational Products
Wang et al. [116] investigated the tableting properties of co-spray dried α-lactose monohydrate, HPMC, and crospovidone. Three particle size grades of lactose (90M, 200M, and 450M) were compared. They found that co-spray drying using grades 90M and 200M produced optimum formulations for tableting. Overall, the tensile strengths of the co-spray dried excipients were larger than those of the corresponding physical mixtures of both compositions. The improvement of compaction was attributed to the presence of HPMC and to the formation of about 30% amorphous lactose during co-spray drying.
Microcrystalline cellulose-rice starch co-spray dried products for direct compression purposes were reported by Limwong et al. [117]. The researchers prepared the co-spray dried mixtures with rice starch compositions of 90%, 80%, 70%, 60%, and 50%. The composition with 70% rice starch was found to be most suitable for direct compression. Co-spray dried powder of this composition had an angle of repose of 37.2° and Carr’s index 19.2%. Flowability was better than several other directly compressible diluents available in the market. Furthermore, the properties of 500 mg tablets (Ø 12.7 mm) of the co-spray dried mixture with 70% rice starch compressed at 8.8 kN load were evaluated. The produced tablets had an average strength of 188.7 N (SD = 8.6), friability 0.6%, and disintegration time 2.56 min (SD = 0.22). These results qualified this co-processed product as a directly compressible excipient [117].
Microcrystalline cellulose-calcium carbonate co-spray dried mixtures were patented by Mehra et al. in 1987 [118]. Different ratios of the two components were suggested as possible combinations. A ratio of microcrystalline cellulose to calcium carbonate of 60 to 40 was proposed. The bulk density of this product was in the range of 0.35–0.45 g/cm3, and the pH of the aqueous slurry in the range 9.5–10. Moreover, the product’s flowability and compressibility profile was better than that of MCC, and exhibited low sensitivity to lubricants.
Li et al. investigated tablet properties of co-spray dried hydroxypropyl methylcellulose (HPMC) with each of mannitol, starch and calcium hydrogen phosphate dihydrate (DCPD) [119]. They employed a center-composite design for optimization employing HPMC (3.5–10.5%) and solid content in feed (19–44%) as independent variables. They found optimal DC co-processed excipient at HPMC compositions of 7.3%, 7.7% and 7.0%, and solid contents in the feed liquid of 44%, 40% and 32% for mannitol, starch and DCPD, respectively.
Another work by Fan et al. [120] attempted to improve the compactability of the bile salts sodium cholate (SC) and deoxycholic acid (DOA) that are used in formulations as absorption enhancers. They co-spray dried SC or DOA with HPMC added at 0%, 2.5%, 5%, and 10% w/w levels. The obtained powders were compressed to tablets (Ø 6 mm) at forces between 50 and 450 kg, and the co-spray dried products were compared with the raw materials and physical mixtures at 10% (w/w) HPMC and 90% (w/w) SC or DOA composition. The produced tablets had tensile strengths between about 0.5 MPa and 6 MPa. Co-spray dried powders of SC and DOC with 10% HPMC demonstrated best compactability profiles. The improved tabletability of the spray-dried powders was attributed to the fine particle size and to the amorphous state of the bile salts after spray drying. In conclusion, co-spraying with HPMC can be a promising strategy to overcome the poor tableting of oral peptide formulations containing large amounts of absorption enhancers.
Vanhoorne et al. [46] co-spray dried mannitol with PVP at percentages of 0%, 10%, and 20%. Co-spray drying of mannitol in formulations with 0% and 10% PVP produced β and α mannitol, respectively. However, spray drying mannitol in formulations with 20% PVP produced mainly δ mannitol. Compaction properties of the co-spray dried powders were compared to physical mixtures. Co-spray dried mannitol with 20% PVP gave the highest tensile strength at all applied pressures.
Saleh et al. [121] spray dried sodium bicarbonate using PVP and silicone oil as auxiliary additives. These additives significantly improved the compressibility of sodium bicarbonate. The prepared co-spray dried combinations showed excellent compressibility and sodium bicarbonate was not transformed into sodium carbonate. Therefore, the superior compression characteristics of the co-spray dried sodium bicarbonate, make it a future candidate in the manufacturing of effervescent tablets by direct compression as a source of carbon dioxide
Although co-spray drying is normally approached as a strategy to improve the tableting properties, some studies have reported no improvement or contrary results. Most of them report a negative impact on the compactability of excipients when surfactants are involved in the co-spraying process.
For example, Roberts et al. [122] prepared spherical spray-dried agglomerates of hypromellose acetate succinate (HPMCAS) alone or in the presence of 1% or 3% sodium lauryl sulfate (SLS). They reported a detrimental impact of co-spray drying with SLS on the tabletability of HPMCAS as compared to the non-processed material.
Bergren et al. [123] investigated the compression behavior of co-spray dried α-lactose monohydrate with polyvinylpyrrolidone (PVP) and polysorbate 80. Τhe concentration of PVP in the ternary blend was 25% w/w and that of polysorbate 80 0.1% w/w. The estimated Heckel yield pressures ranged between 94 MPa and 127 MPa for all co-spray dried powders compared to 87 MPa for spray-dried lactose powder (amorphous lactose). The presence of polysorbate 80 in the co-spray dried powders decreased the tensile strength over the applied compression pressure range (1–6 MPa). The compactability of tablets of co-spray dried lactose with PVP was similar to that of spray-dried lactose alone. Similar observation on the effect of polysorbate 80, as a co-excipient, on the compactability of amorphous lactose particles prepared by spray drying was found by Fichtner et al. [124]. They reported a positive correlation between the dispersive surface energy of spray-dried powders and tensile strength of their compacts prepared at constant porosities.
Co-spray drying of lignin with sodium lauryl sulfate (SLS) for improved compaction behavior of lignin was investigated by Solomon et al. [125]. The researchers prepared co-spray dried powders of lignin that included SLS at 0%, 5%, 10%, and 15% levels. Although the Heckel yield pressure and elastic recovery decreased with increasing SLS percentage, a decrease of tensile strength with increasing SLS content in the compositions was noted, attributed to the adsorption of surfactant at the droplet surface, thus reducing interparticle bonding and resulting in poor compaction and capping.
7. Multifunctional Co-Spray Dried Excipients
7.1. Direct Compression and Sustained Release
7.1.1. Kollidon® SR
Kollidon® SR is a co-spray dried powder composed of 80% Polyvinyl acetate (MW~450,000), 19% PVP (K 30), 0.8% SLS and 0.6% w/w silica. It is composed of roundish particles with an average diameter between 80 and 100 µm and good flowability (angle of repose < 30°) [126]. The glass transition temperature is low (around 40–45 °C) and thus deforms mainly plastically [127,128]. Several studies have demonstrated its suitability as a matrix former for sustaining drug release by direct compression tableting [128,129,130,131,132], and the release is independent of the compression force [131,133]. Kollidon® SR and its mixtures with theophylline monohydrate exhibited higher compactability than MCC and corresponding mixtures [134].
7.1.2. Investigational Products
Lactose–sodium alginate co-processed excipient was produced by spray drying an aqueous solution of α-lactose monohydrate and sodium alginate (SA) at SA contents up to 30%. The spray-dried composite particles had excellent micrometric properties as a filler for direct tableting and good compactability. The matrix-tablets prepared from the composite particles showed slower drug release than the physical mixture of lactose and SA particles at the same lactose/SA ratio. The release was more retarded in acidic (pH 1.2) than in neutral solution (pH 6.8) due to the pH-dependent swelling of SA [8,135].
7.2. Direct Compression and Oral Disintegration
7.2.1. F-MELT®
F-MELT is a co-spray dried product based on the carbohydrates xylitol and mannitol, disintegrant (crospovidone and MCC) and inorganic component. It is available in two grades, named C and M. The former grade contains magnesium aluminometasilicate (Neusilin®) as the inorganic component, and the latter contains calcium hydrogen phosphate anhydrous (Fujicalin®). It has a good mouthfeel sensation and is designed for orally disintegrating tablets (ODTs) and soft chewable tablets. It provides high drug stability due to non-hygroscopicity and neutral pH, high flowability due to the dense isodiametric particles, excellent tablet hardness, low friability and high drug loading. It does not cause capping or sticking during compression [136,137].
7.2.2. PEARLITOL® Flash
PEARLITOL® Flash is a co-spray dried mixture of mannitol (80–85%) and maize starch (15–20%). It is composed of isodiametric particles with a 200 µm mean diameter and about 1.8% moisture content. PEARLITOL® Flash disintegrates rapidly, providing a smooth texture making it suitable for ODT Pharmaceutical and/or Nutraceuticals formulations [138].